An innovative approach towards standardizing cell therapy manufacturing
Learn about Thermo Fisher Scientific’s modular, fit-for-purpose platforms designed specifically to meet the requirements of cell therapy manufacturing right now, and in the future.
11 Sept 2022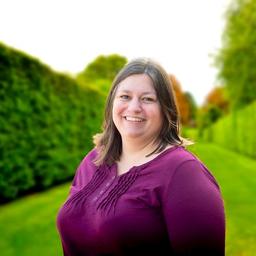
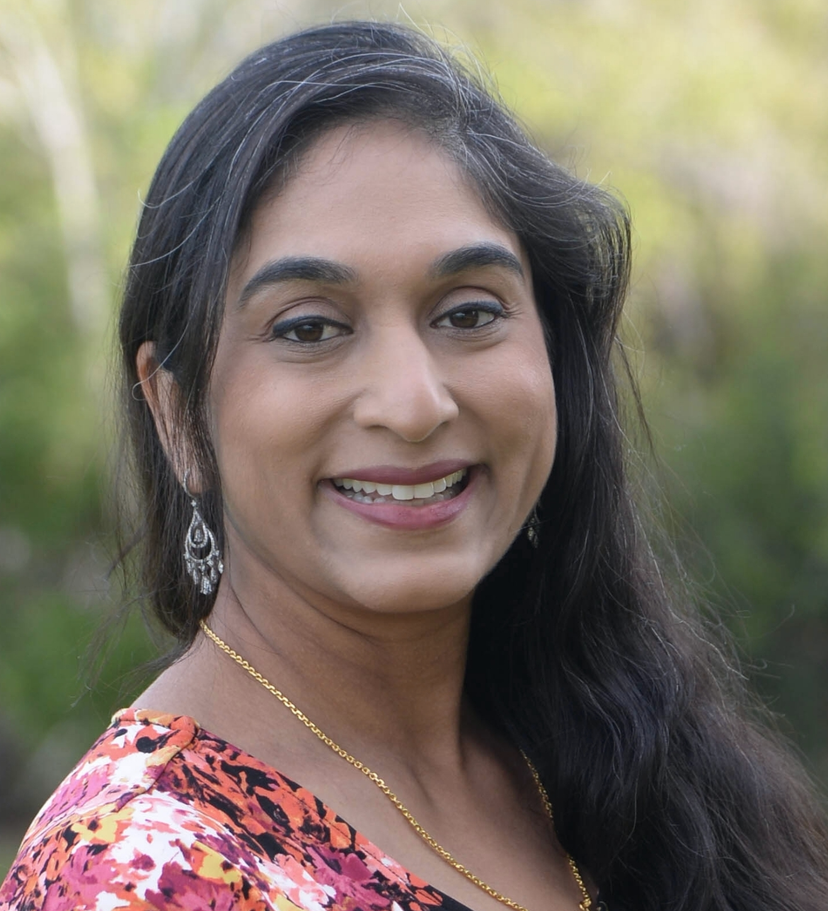
Cell therapy manufacturing is a constantly evolving process. Initially developed through the adaptation of existing tools and technologies from other workflows, it is abundantly clear that there is a need for specialized tools to support standardization as the field continues to move forward.
Dr. Shikha Mishra, Technical Workflow Lead for Cell and Gene Therapy at Thermo Fisher Scientific, speaks to SelectScience® about recent technologies designed specifically for cell therapy manufacturing applications.
Dr. Mishra explains some of the challenges that cell therapy manufacturers face, “The cell therapy manufacturing workflow is a complex, multi-step process. It is very labor intensive with several open processes, making it prone to error and contamination. This contributes to a high manufacturing failure rate, which can significantly impact the cost of the therapy. There are a number of steps where things could go wrong, and cell therapy manufacturing is essentially a zero-failure tolerance setting.”
For treatments such as autologous CAR-T cell therapy that use an individual patient’s cells, there is an inherent variability built into the process. Therefore, any solutions that support cell therapy manufacturing also need to support flexibility while mitigating risks.
A modular, fit-for-purpose system
To address these challenges and support standardization of workflows, Thermo Fisher has developed a modular, fit-for-purpose portfolio of instrumentation and products. The aim is to support cell therapy manufacturers from end-to-end with a closed and flexible solution that can be customized to meet their needs.
“Over the past few years, Thermo Fisher has developed several instruments that span key elements of the workflow, specifically designed with the cell therapy manufacturer in mind,” says Dr. Mishra. These instruments enable customers to ‘close’ their process, reducing the risk of contamination at contact points, and thereby increasing manufacturing success.
Dr. Mishra elaborates on how these modular devices work together, “All of the instruments in the Cell Therapy Systems (CTS) portfolio are compatible. They have been designed to be physically compatible and digitally integratable.” As Dr. Mishra explains, “We have an off-the-shelf software product called Gibco™ CTS™ Cellmation, which allows customers to integrate individual instruments within a common Delta V™ network, using the same operator interface for consistency. What this allows for is a more automated process that also enables maintenance of your data integrity. Importantly, the ability to automate simplifies the workflow steps and reduces labor and manual manipulation. By using closed instrumentation and single use kits, you can reduce contamination and human error, which lends itself to a more reproducible and robust manufacturing process.”
Dr. Mishra shares one example of an instrument from the cell therapy portfolio. “Across the manufacturing workflow, we have instrumentation specialized for each unit operation. The Gibco™ CTS™ Xenon Electroporation System is our newest instrument. It is comprised of the instrument, electroporation chamber or cartridge, current good manufacturing process (cGMP) manufactured buffers, and software. This instrument is closed, flexible, modular, and enabled for digital integration; most importantly, it is designed to scale to address current autologous needs and future allogeneic workflows.”
Dr. Mishra summarizes the advantages that Thermo Fisher’s new cell therapy instruments will bring. “From the outset of your manufacturing process, you will be able to close and automate your workflow all the way through to cell expansion. These innovative solutions minimize manual processing, reduce contamination and ultimately create a safer and more cost effective product.”
These tools are designed to meet the challenges of cell therapy manufacturing today and built to scale for future needs and support manufacturers at every stage of the development pipeline. As Dr. Mishra explains, “Instrumentation needs to scale in order to support a range of clinically relevant volumes. It is not just the autologous single patient model anymore; we need to support the evolution of the field. So, we are developing solutions that can meet commercial needs and support allogeneic and emerging therapies that are up and coming.”
Collaborating with biotech and pharma to develop the right solutions
Notably, these technologies are not created in a vacuum. As part of the development process, Thermo Fisher has collaborated with cell therapy manufacturers across biotech and pharma, and continues to do so. This helps to bridge the transition between early discovery and late-phase development, while also ensuring that the instruments are built to support the needs of cell therapy manufacturers.
When designing a fit-for-purpose solution, if you remain cognizant of the customer needs, that's how you are going to drive success.
Dr. Shikha Mishra Thermo Fisher Scientific
Dr. Mishra shares the way that collaborations have enhanced the design of these instruments, and how these collaborations are benefiting cell therapy manufacturers, “We're not just a tools provider in the way that we're not just selling you glue to fix your problem. We are actually developing many different types of glue to solve your specific problems. If you collaborate with us, you gain access to our team of scientists and engineers that have experience and expertise, and who are the ones developing these new technologies.”
There are significant benefits for both sides, attests Dr. Mishra, “It is really about that collaborative process optimization. You get effective tech transfer, effective integration of our technologies into your manufacturing process, and this leads to a very high-quality manufacturing output. We also provide product-specific regulatory support to enable your regulatory filings. What we gain as a collaborator are your insights and learnings, and importantly, we can observe how you are actually utilizing and implementing our technologies. This allows us to continuously develop relevant solutions and products to support our customers.”
These collaborations are ongoing, helping to facilitate the challenging transition of moving therapies through the commercialization pipeline. As cell therapy manufacturing evolves, so will the systems to support them.
“It's definitely a two-way communication street,” concludes Dr. Mishra. “When designing a fit-for-purpose solution, if you remain cognizant of the customer needs, that's how you are going to drive success.”
Whether you are just getting started or facing unexpected roadblocks along the journey, Thermo Fisher’s experienced scientists and engineers can work alongside your team to help optimize your process. Learn more about Thermo Fisher’s cell therapy collaboration program, or request information.
Read more about the latest in cell and gene therapy in our Special Feature >>