Futureproof lab automation with dynamic robotics
Explore the evolving role of robotics in lab automation, from repetitive tasks to dynamic workflows
29 Feb 2024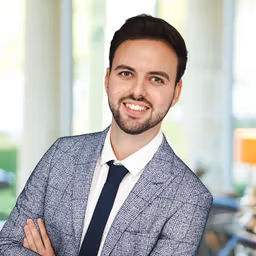
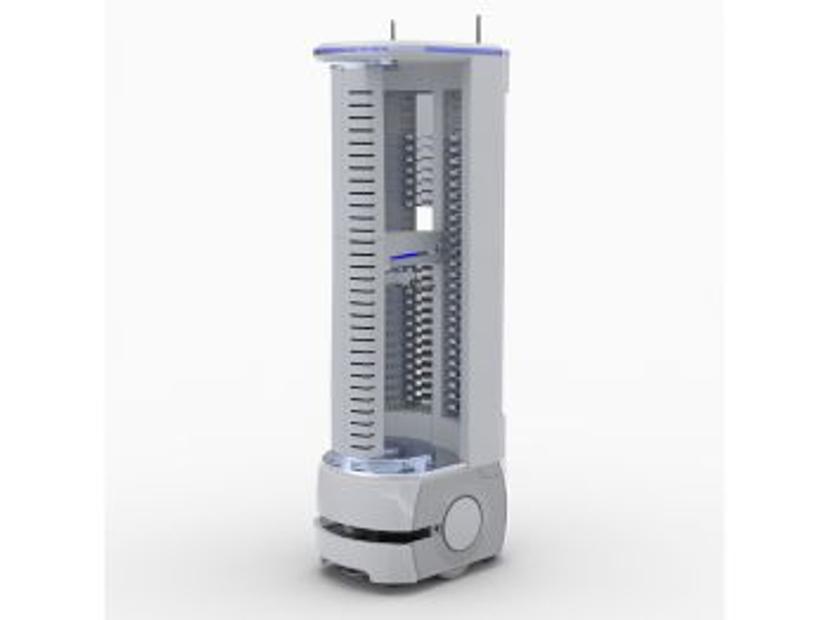
The role of robotics in lab automation has evolved in recent years from primarily being utilized for repetitive tasks to taking on a more strategic role within the lab. In the Lab of the Future, robotics will go beyond reducing repetitive tasks to automating increasingly complex dynamic and distributed workflows.
Envision labs where workflows are optimized, experiments are conducted with unparalleled speed, and the pursuit of scientific breakthroughs becomes a thrilling adventure. A future where the pages of discovery are turned not by hands alone, but by the synchronized dance of technology and ambition.
Speaking with Shaival Desai, Product Manager – Lab Automation Hardware, Thermo Fisher Scientific, we explore the success criteria for implementing laboratory automation and unveil an innovative robotics solution designed to meet the requirements of the Lab of the Future.
“Laboratories have come to realize the need for automation and are recognizing the value of strategically adopting laboratory robotics,” explains Desai. “In the past, laboratories have not been investing in future-proof solutions. Automation solutions have typically lacked the flexibility for easy reconfigurations with no user-friendly solution for automating distributed workflows or the ability to repurpose automation capabilities."
The Thermo Scientific™ Autonomous Mobile Robot (AMR) with the Thermo Scientific™ Spinnaker™ 3 Microplate is a a seamless fusion of advanced robotics and artificial intelligence, designed to navigate the intricate landscapes of laboratories with unparalleled precision. This mobile marvel heralds a new era for contract research organizations (CRO), big pharma, and biopharma companies alike. The Thermo Scientific AMR solution transcends the limitations of traditional benchtop robotic systems, offering a transformative synergy of flexibility, adaptability, and efficiency.
These types of solutions are well-positioned to overcome these issues offering a reconfigurable laboratory automation platform that can improve instrument utilization and the efficiency of lab space.
The evolving needs of modern laboratories
Whilst the approach to automation has shifted in recent years, some key requirements of automation solutions have remained constant. “Reliability and uptime of the automated solution are still paramount,” explains Desai. “The solution should not require more oversight and effort than the output that it generates. Additionally, as with any investment, a critical criterion is a high return on investment. For this, robotic automation solutions must be space and resource-efficient.”
Lab robotics have been evolving slowly over time, but they are still a long way away from not needing any technical skills at all, “Lab staff still need to be trained, and retaining or scaling that knowledge within an organization can be a challenge due to the specific nature of the skills required.”
Another focal point for many labs looking to invest in future-proof automation solutions is reliable and safe connectivity across instruments, systems, and labs. “Physical and digital connectivity that's reliable as well as safe is a focus point for labs today. This comes with the latest shift to automated distributed workflows instead of simply focusing on very high-throughput dedicated automation systems.” A big driver behind this shift is also the increased focus on biologics automation which is by nature more dynamic than traditional small molecule drug discovery.
Automation solutions used to be these fixed systems that would only do one thing over and over for long periods. Futureproofing by incorporating connectivity and modularity that allows for reconfigurations of the system, sharing of resources and floor space, as well as being able to execute distributed workflows is now key. In an extreme case, as labs' needs evolve, they might also be looking at completely repurposing their existing automation solution, this is all part of futureproofing and ensuring high return on investment.
Dynamic lab automation made possible
The key needs of a dynamic lab are: Walk-away confidence for 24/7 unattended operation, ease to scale, and speed of deployment thereby maximizing returns.
The auto-leveling capability of the Spinnaker 3 automatically corrects for the nest position and level, removing the burden of having to repeatedly teach the robots. This makes the process much more efficient.
Shaival Desai
Thermo Fisher Scientific
Thermo Fisher Scientific aims to meet the evolving connectivity, modularity, and future-proofing criteria required for modern laboratory automation. “As we see more connected workflows becoming commonplace in many laboratories, we see that more instruments are moving around instead of being stationed in one place for long periods,” states Desai. “There is an issue with the current robotic solutions on the market in that it requires skilled users to be able to reteach all the new instrument locations as well as make sure that all the instrument nests are co-planner so that the sample transfer is reliable. The auto-leveling capability of the Spinnaker 3 can automatically correct for the nest position and the nest level, removing the burden of users having to master the skill of robotic teaching. This allows for effortless modularity and reconfigurability of the automation solutions.”
Additionally, workflows often require the scanning of barcodes on microplates for sample tracking. When instrumentation in the lab is moved around, reconfigured, or repurposed and this barcode reader is separate from the robot, a lot of user skill and effort is required to reconfigure the whole system. The Spinnaker 3 overcomes this challenge with its built-in barcode reading capability.
Many instruments and storage devices do not uniformly adhere to a specific orientation for sample storage or nest placement. It is therefore inevitable that throughout a workflow there will be a need to adjust the plate's orientation. This is particularly true in modular and reconfigurable systems where there is limited control over the orientation of these instruments. “The inclusion of the re-grip nest within the Spinnaker 3 resolves this issue by ensuring that the re-gripping capability moves seamlessly with the mover,” says Desai. “Users are relieved of the need for additional efforts to set up, teach, or utilize the re-grip, as it happens automatically.”
The Spinnaker 3 is well suited for a variety of applications including high-throughput repetitive workflows. Combined with all the reliable connectivity capabilities such as the vision-based position teaching, the auto-leveling, built-in barcode reading, and re-gripping capabilities, it is also ideal for distributed workflows as well as small-scale automation solutions that users might want to set up by themselves. The ease of teaching and the error-proofing that is built into the Spinnaker 3 makes it suitable for all kinds of different workflows and lab environments such as synthetic biology, and automating biologics discovery and development.
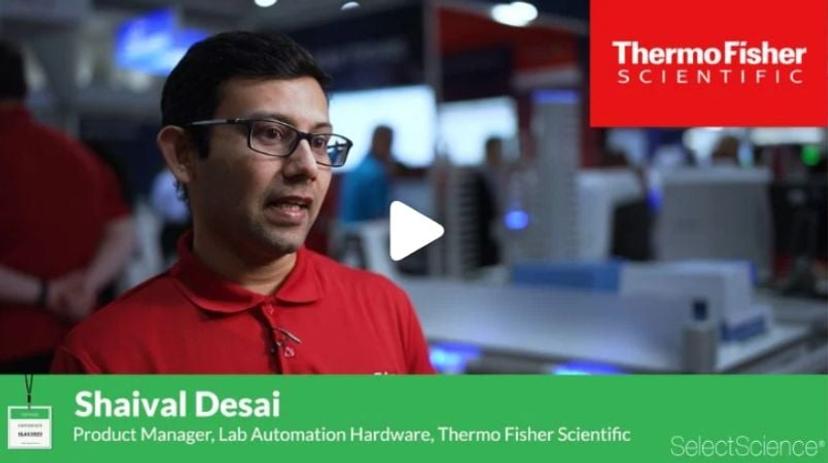
How to meet the requirements of the Lab of the Future
Looking to the future, the next frontier of physical connectivity for laboratories will involve mobile robotics. Desai concludes, “Mobile robotics can move independently without tracks or paths, saving deployment costs. These robots can also be outfitted with collaborative robotic arms to form a highly flexible and safe mobile robot solution connecting workstations within and between labs to create a seamless workflow. However, this introduces an additional layer of complexity as there is limited control over the orientation, leveling, and teaching of these instruments. Spinnaker 3's features, including vision-based position teaching and the ability to auto-correct the nest location while simultaneously aligning with the instrument level, position it as an ideal choice for mobile robotics applications.”
“The Spinnaker 3 aligns seamlessly with the future endeavors of labs, addressing the evolving requirements of connectivity, modularity, and futureproofing. By reducing the burden on users to learn robotics, reducing training needs, and providing a solution that is reliable, safe and efficient, Spinnaker 3 aims to play a pivotal role in shaping the future of laboratory automation.”