Novel clarification technology addresses biologic manufacturing bottlenecks
Learn how Solventum’s scalable chromatographic clarification platform is helping to meet the growing demands of modern bioprocessing
31 Mar 2025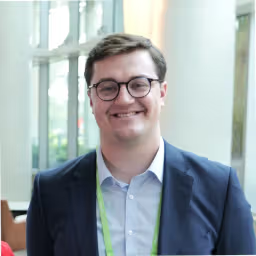
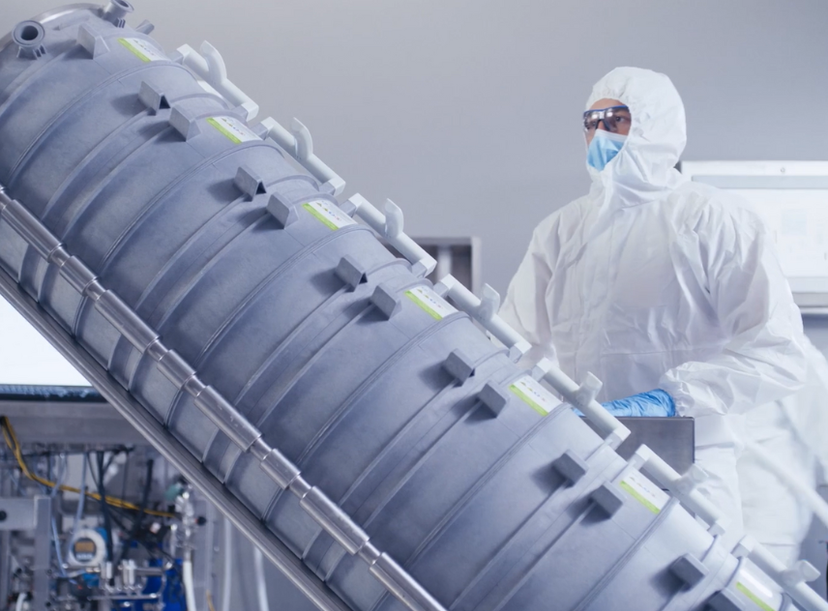
“We’re going to see a shift away from older paradigms,” Dr. Alexei Voloshin, Global Head of Bioprocess Science at Solventum, explains, “and the new processes that emerge will be far more effective.”
As the demand for biologic drugs increases and therapeutic modalities become more complex, manufacturers are facing increasing bottlenecks in their production processes. One of the most pressing challenges is the clarification of cell cultures — a crucial step in which cells, cell debris, and other impurities are removed from cell culture fluids prior to downstream processing.
The rising complexities in biologics, driven by new therapeutic modalities such as gene therapies, viral vectors, and mRNA-based treatments, as well as increasing cell densities in biopharma manufacturing, are placing unprecedented pressure on traditional harvest and clarification processes. Manufacturers are grappling with inefficiencies, yield losses, and scalability issues, forcing the industry to seek innovative solutions.
“Process intensification is one of the major megatrends in the industry today,” says Dr. Alexei Voloshin, Global Head of Bioprocess Science at Solventum. “We are accelerating that trend by developing new technologies that both improve on the existing operations and help the industry implement radical new strategies for bioprocessing.”
Addressing today’s challenges with clarification
Traditionally, clarification technologies have focused on the removal of insoluble impurities– such as cells, cell debris, and other aggregates — through either size-based filtration or density-based centrifugation. However, both methods have inherent limitations, particularly in handling high cell density cultures and newer biologic modalities. They also struggle to remove soluble impurities, such as host cell proteins and DNA, with the precision needed in modern biologics production.
“Neither of these traditional approaches allows for the high-fidelity separation of soluble impurities from products,” Voloshin notes. This challenge has only intensified with the need to process larger volumes at commercial scales while maintaining the flexibility to adapt to the production of diverse biologics.
To address these issues, Solventum has developed the 3M™ Harvest RC Chromatographic Clarifier platform, a next-generation harvest and clarification solution designed to meet the demands of high cell density cultures, while providing scalability and flexibility across different bioprocessing process and product workflows.
“We developed the unified system of 3M™ Harvest RC and 3M™ Harvest RC Centrate Chromatographic Clarifiers to give the industry the ability to remove both soluble and insoluble impurities with the fidelity that people expect out of chromatography,” explains Voloshin. “These technologies are making processes far more productive and flexible, providing improved product yield, higher quality clarified fluid, and a streamlined approach to clarification process development.”
Drastically simplifying the clarification process
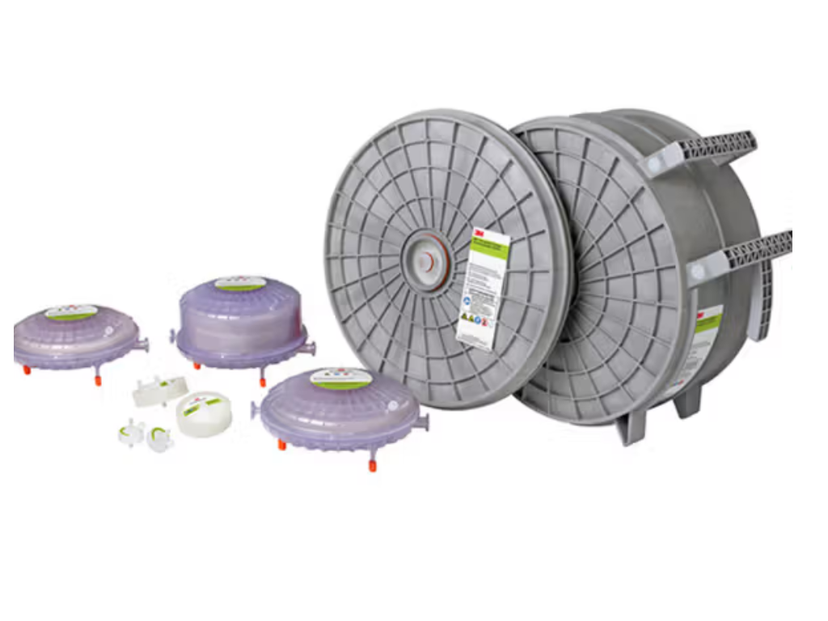
3M™ Harvest RC Centrate Chromatographic Clarifier is a single stage single-use chromatographic clarification solution designed to effectively clarify modern cell culture centrates.
At the core of the 3M™ Harvest RC Chromatographic Clarifier is synthetic fibrous anion exchange (AEX) media made possible by the functionalization of a non-woven fiber material with quaternary amine (Q)-chemistry. This unique design enables the system to remove both insoluble and soluble impurities in a single step, drastically simplifying the clarification process. The functionalized non-woven media for the 3M™ Harvest RC Centrate Chromatographic Clarifier has been designed to address centrate feed streams and also incorporates a Q-functional polyamide membrane.
“We’ve reinvented the traditional membrane and media by functionalizing both parts,” explains Kuan-Yin Lin, Product Development Specialist for the Solventum Harvest platform. “By combining size-based and charge-based separation, we can remove multiple impurities that customers previously struggled with — and do it all in one single device.”
The platform’s ability to simultaneously perform size- and charge-based separations provides several key benefits, including enhanced product recovery, with yields exceeding 95%, and superior impurity removal, including a reduction of DNA levels to less than 500 ppb. These single-stage clarification devices also reduce the need for multiple filtration or separation steps, improving downstream efficiency and minimizing yield losses.
Improved flexibility and scalability
One of the standout features of the 3M™ Harvest RC Chromatographic Clarification platform is its ability to scale across different process and product workflows as well as production footprints. Whether a manufacturer is operating small-scale bioreactors for early-stage development or large-scale commercial facilities, the chromatographic clarification platform is designed to suit various production scales and can accommodate both direct harvest and clarification as well as centrate clarification processes.
“The 3M™ Harvest RC Chromatographic Clarification platform is scalable from drug discovery all the way to commercial production,” explains Elliott Zell, Global New Product Marketer at Solventum. “The 3M™ Harvest RC Chromatographic Clarifier and 3M™ Harvest RC Centrate Chromatographic Clarifier are two options for biologic producers that can either be used in direct harvest or centrate clarification processes and produce clarified fluid with comparable quality. This really helps streamline process development efforts, improve process economics and ultimately increase speed to market.”
Sustainability and expanded accessibility
In addition to performance advantages, the 3M™ Harvest RC Chromatographic Clarification platform offers notable sustainability benefits – an increasingly critical priority for biopharmaceutical companies. The platform’s design cuts down on resource consumption, requiring up to 50% less water for a pre-conditioning rinse when compared to traditional depth filtration processes.
“The process we’ve developed uses significantly less water and energy as well as leaving a much smaller footprint in terms of materials used for separations,” notes Voloshin. For biologics manufacturers, this translates to a reduced environmental impact and lower overall operational costs.
Beyond sustainability, the platform’s efficiency also enables greater accessibility. “This allows us to complete more processes with the same resources, but just as importantly, to build processes in regions where resource limitations have made that difficult in the past,” Voloshin adds. “This means we can now deliver vital medicines to areas that were previously out of reach.”
The future of bioprocess clarification
As new biologics are developed and existing products are produced in higher quantities, the demand for robust and adaptable clarification systems is set to increase. The 3M™ Harvest RC Chromatographic Clarifier platform marks a significant advancement in bioprocessing, but its development is far from complete. As new challenges continue to emerge, Solventum is committed to refining its chromatographic clarification technology and expanding its capabilities to meet bioprocessing needs.
“Because it's a brand-new technology and a brand-new approach, we are actively gathering feedback from customers to understand their needs,” says Lin. “With this input, we will continue to innovate and expand our platform to meet the evolving demands of the industry.”
One of the most promising aspects of this next-generation platform is its ability to customize filtration membranes and anion exchange media to target specific impurities, opening the door to meet the unique requirements of various processes. This flexibility promises even more specialized and efficient clarification solutions in the future.
“We’re going to see a shift away from older paradigms,” Voloshin explains, “and the new processes that emerge will be far more effective.”
“The next generation of bioprocesses will take advantage of these new technologies, addressing the major trends of today and tomorrow,” he concludes.